大跨径连续箱梁裂缝修补技术研究
点击数:898
发布时间:2017年8月10日 来源:
[摘要]混凝土由于细微裂缝的出现及将来可能继续扩展,水及潮湿空气会侵蚀钢筋,从而影响混凝土结构的耐久性,同时会影响结构的承载能力。为保证混凝土结构的耐久性和钢筋不被锈蚀,必须对裂缝采取有效的方式进行修补。结合某铁路大桥连续梁跨中横隔板裂缝修补施工实践,介绍了环氧树脂胶低压灌注封堵及粘贴碳纤维布施工工艺。
1 工程概况
某铁路大桥跨越地方公路,采用( 40 + 56 + 40) m连续梁桥一次跨越( 见图1) ,与某公路斜交角76°,两主墩墩号分别为1 号和2 号,采用钻孔灌注桩基础,每个主墩为10 根直径1. 5m 钻孔桩,边墩为10 根直径1. 25m 钻孔桩; 上部主梁结构采用挂篮悬臂浇筑法施工。
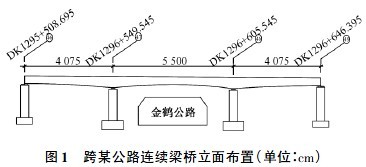
箱梁截面为单箱单室截面变高度、变截面结构,箱梁顶板宽12. 0m,厚度除梁端附近外均为40cm,底板宽6. 7m,厚度为40 ~ 80cm。腹板厚度为48 ~ 80cm,梁体采用C50 混凝土。如图2 所示。
2 箱梁裂缝简介
某铁路大桥( 40 + 56 + 40) m 连续梁采用挂篮悬臂浇筑法施工,2009 年11 月15 日跨中合龙,在合龙段等强并张拉完成拆除挂篮时,发现跨中合龙段横隔板处有裂缝,裂缝呈竖向,深度沿顺桥向,初步判断裂缝宽度和深度已超出允许范围。
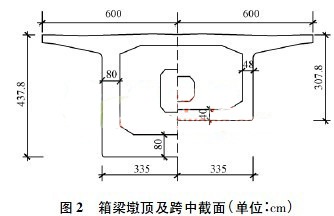
3 箱梁裂缝检测
裂缝检测委托具有裂缝检测资质的检测机构进行,对裂缝的宽度和深度依据有关检测技术规范及标准进行专业检测。
3. 1 裂缝宽度检测
裂缝宽度检测采用裂缝测宽仪进行,测宽仪型号为DJCK—2,检测前须确认仪器检定日期在有效期内。针对每条裂缝选取3 个点进行测量,分别测量读数,最后计算出裂缝的平均宽度。
现场实测裂缝宽度检查结果如表1 所示。
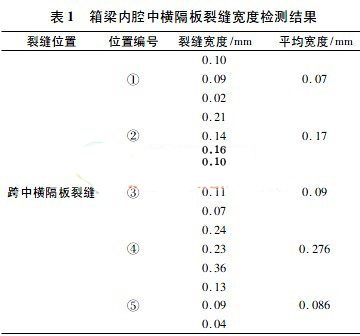
3. 2 裂缝深度检测
裂缝深度检测采用非金属超声波裂缝测深仪进行,测深仪型号为NM - 4A,检测前须确认仪器检定日期在有效期内。针对每条裂缝选取3 个点进行测量,分别测量读数,最后取深度的最大值。
根据现场检测结果,中横隔板处裂缝深度为贯通裂缝。如图3 所示

3. 3 裂缝检测结果
该桥连续梁跨中合龙段中横隔板处产生5 条裂缝,裂缝宽度分布在0. 070 ~ 0. 276mm,且均为贯通裂缝,综合分析确定为收缩裂缝。
4 箱梁裂缝产生原因
该铁路大桥连续梁之所以在跨中合龙段中横隔板处产生收缩裂缝,经综合分析,主要原因有以下几方面: ①跨中合龙段施工正处于11 月份,属冬季施工,箱梁内腔内温度较低,内腔内冬季施工未采取有效的养护方式。②中横隔板属大体积混凝土施工,没有采取有效的温控措施。③受架梁节点工期紧逼,跨中合拢段合龙前墩顶临时锚固未完全解除约束,体系未完成转换。④跨中合龙段中横隔板未设计横向预应力。
5 箱梁裂缝修补技术
某铁路大桥( 40 + 56 + 40) m 连续梁合龙段跨中箱梁横隔板施工完成后出现了5 条裂缝,检测表明,宽度约0. 070 ~ 0. 276mm,均为贯穿裂缝,经初步分析为混凝土收缩裂缝,根据检测单位和多方专家的建议,对于中横隔板裂缝采用灌缝处理方式进行修补。
混凝土由于细微裂缝的出现及将来可能继续扩展,水及潮湿空气会侵蚀钢筋,钢筋锈蚀影响混凝土结构的耐久性,同时会影响结构的承载能力。为保证混凝土结构的耐久性和钢筋不被锈蚀,采用灌浆封缝封堵方式进行裂缝修补; 同时考虑到铁路振动荷载影响,灌浆封缝封堵完成后在表面粘贴碳纤维布加强,提高抗拉强度,保证混凝土的质量及整体性,避免再次出现裂缝。
5. 1 环氧树脂胶低压灌注封堵
5. 1. 1 修补步骤
裂缝修补主要采用具有低黏度、高强度和高流动性的环氧树脂胶进行低压灌注封堵。其主要步骤如下: ①寻找裂缝找出裂缝位,并标出裂缝位置。②混凝土表面打磨处理用钢丝刷对裂缝两侧混凝土表面打磨,粗糙结构表面,便于封缝,打磨方向为顺裂缝方向,打磨范围为裂缝两侧各60mm; ③混凝土表面灰尘清理用钢丝刷清理表面已打磨的混凝土表面,然后擦净结构表面灰尘; ④埋设灌浆嘴在混凝土裂缝上部埋设注胶底座,埋设间距≤300mm,且每个裂缝转折点要埋设一个,每条裂缝至少要埋设2 个注胶底座,注意注胶底座埋设不能堵塞缝口,以免注胶困难; ⑤结构胶封缝用快速封缝胶将其他部位的缝口封堵密实。
5. 1. 2 压力注胶材料及机具
1) 灌浆机具灌浆机具采用CZ - 自动压力树脂注入器,是袖珍式灌浆机具,操作方便、灵巧、轻便,可对任何方向的裂缝及空鼓部位进行灌浆,灌浆的质量有可靠保证。凡混凝土不密实和连通的始发裂缝及空隙,树脂会自动填满,并能沿钢筋方向渗透到混凝土密实处。
2) 灌浆材料低黏度改性环氧树脂采用双组分低黏度改性环氧树脂,甲、乙组分,采用低黏度环氧树脂具有可灌性、韧性好、强度高、有效操作时间长的特点,该灌浆树脂的抗压强度≥40. 0MPa,抗拉强度≥3. 0 ~6. 0MPa,裂缝修补完成后强度高于原主体结构,可达到裂缝修补效果。
5. 1. 3 压力注胶工艺
1) 当树脂固化达到一定程度后,进行压力灌浆,灌浆工艺采用全封闭保压注浆法工艺。当注浆产生压力时,由于树脂的进入,空气排出,树脂进入混凝土裂缝间隙并充满。由于灌浆时利用混凝土毛细管作用,0. 05mm的间隙均能进入。凡是混凝土有裂缝处,树脂都会自动填满,混凝土间隙灌满后,注入器便会自动停止灌浆。保持一定压力时间后( 大约12 ~ 24h) ,拆除注入器,树脂不再流出,随时间的增加,树脂逐步固化,强度不断增加。
2) 灌浆结束后,凿掉预埋注浆口。
5. 2 粘贴碳纤维布施工
经灌缝处理,环氧树脂固化后,进行粘贴碳纤维布加强施工。粘贴方式: 沿裂缝方向贴宽度0. 4m 宽的碳纤维布,布的纤维方向与裂缝垂直,如裂缝较密或间距较小时,可整面粘贴碳纤维布。
5. 2. 1 基底处理
粘贴碳纤维布前,混凝土的表面应按以下的方法
进行处理: ①原混凝土的粘合面,用硬毛刷沾高效洗涤剂,刷除表面油垢污物后用冷水冲洗,再对粘合面进行打磨,除去1 ~ 2mm 厚表层,直至完全露出新面,用压缩空气除去粉尘或用清水冲洗干净,待完全干燥后用脱脂棉沾丙酮擦洗表面即可。②对于修补出现的新混凝土结合面,先用钢丝刷将表面松散浮渣刷去,再用硬毛刷沾洗涤剂洗刷表面,或用吸尘器、吹风机之类清除表面,或用有压冷水冲洗,待完全干燥后即可涂刷黏结剂。③混凝土表面有孔洞时,先凿掉其表面混凝土的薄弱层及松动石子。清除碎渣,并用水冲洗干净,待干燥后,配制强度比原混凝土强度高一级以上的环氧树脂胶修补。④石子的不平整混凝土表面,需将表面凸出的石子凿掉,用混凝土角磨机将构件基面的混凝土打磨平整,基本平整后,按普通混凝土的表面要求处理。
5. 2. 2 涂底胶
1) 按一定的比例( 一般采用主剂: 固化剂= 2∶ 1)将主剂与固化剂先后置于容器中,用台秤计量,人工搅拌均匀搅拌,根据现场实际气温决定用量并严格控制使用时间。保证在1h 内用完。
2) 用滚筒刷将底胶均匀涂刷于混凝土表面,待胶固化后( 固化时间视现场气温而定,以指触干燥为准)再进行下一道工序施工。
5. 2. 3 找平
1) 用刮板精心涂刷、括平,保证混凝土表面平整。
2) 混凝土表面凹陷部位应用FE 胶填平,模板接头等出现较大高度差且无法打磨平的部位应用FE 胶填补,形成过渡坡度,尽量减少高度差。
3) 转角处也应用FE 胶修补成光滑的圆弧,半径≥10mm。
5. 2. 4 粘贴
1) 待找平层FE 胶固化后( 以指触干燥为准) ,进行碳纤维布粘贴。
2) 按设计要求的尺寸及层数裁剪碳纤维布,除非特殊要求,碳纤维布长度一般应在3m 之内。
3) 调配、搅拌粘贴材料FR 胶( 使用方法与底胶FE 相同) 。然后均匀涂抹于待粘贴的部位,在搭接、混凝土拐角等部位要适当多涂刷一些,涂层保持均匀,厚度基本一致。
4) 粘结碳纤维布,在确定所粘结部位无误后剥去离型纸,用特制流滚子反复沿纤维方向滚压,去除气泡,并使FR 胶充分浸透碳纤维布。多层粘结应重复上述步骤,待碳纤维布表面指触干燥方可进行下一层的粘结。
5) 在最后一层碳纤维布的表面均匀涂胶撒上沙子便于粉刷处理( 等强后可在碳纤维布表面涂抹一层素混凝土) 。
6) 碳纤维布沿纤维方向的搭接长度按设计要求≥200mm. ,搭接处保证粘结牢固,不得出现空鼓。
5. 3 裂缝修补质量控制要点及注意事项
5. 3. 1 裂缝修补质量控制要点
1) 施工过程中,严格按照施工方案的技术要求逐道工序验收合格后方可进行下道工序。
2) 应重点检查灌浆是否饱满。
3) 应重点检查碳纤维布粘贴是否空鼓。
5. 3. 2 裂缝修补注意事项
1) 所用材料要密闭保存,避免受潮影响施工质量。
2) 现场施工人员在处理混凝土表面时应穿工作服,佩戴防护眼镜、口罩和手套。
3) 与施工配套的脚手架要有足够的安全性。
4) 须有材料的生产厂家所提供的材料证明。
5) 现场配制的封缝、涂刷材料,应现配现用,不得一次配置,分批使用; 各组分称量准确,严格按照配比设计要求。
6) 每一道工序结束后均应按工艺要求进行检查,并做好相关的验收记录,如出现质量问题,应立即返工。
6 预防措施
大跨度连续箱梁在后续高速铁路建设过程中将被广泛应用,一般采用挂篮施工工艺为首选,如何有效预防合拢后跨中及墩顶横隔板处的裂缝出现是一个重要的课题,通过某铁路大桥( 40 + 56 + 40) m 连续箱梁跨中横隔板裂缝的修补过程,提出以下建议。
1) 混凝土浇筑完毕后,箱梁内腔养护作为一个薄弱环节应重点控制。
2) 横隔板大体积混凝土施工应采取有效温控措施。
3) 合龙段浇筑前,体系转换要按设计要求完成。
4) 向设计单位建议在未设置横向预应力的横隔板处增设横向预应力。
7 结语
某铁路大桥( 40 + 56 + 40) m 连续箱梁跨中横隔板裂缝已于2010 年1 月25 日修补完成,2010 年2 月4日架桥机顺利通过并进行了应力应变监控,各项指标均在设计范围内,情况良好。截止2010 年5 月25 日,经过近4 个月的持续观察,裂缝修补后原裂缝未出现裂纹且周围无扩展延伸趋势,充分证明了裂缝修补施工工艺各项指标均达到了预期效果。该连续梁中跨横隔板裂缝修补施工工艺的成功实施,对今后出现类似问题的解决具有较强的指导意义。
参考文献:
[1] 铁道部经济规划研究院. TZ216—2007 客运专线无砟轨道铁路工程施工技术指南[S]. 北京: 中国铁道出版社, 2007.
[2] TB10002. 1—2005 铁路桥涵设计基本规范[S]. 北京: 中国铁道出版社,2005.
[3] TB10002. 3—2005 铁路桥涵钢筋混凝土和预应力混凝土结构设计规范[S]. 北京: 中国铁道出版社, 2005.